TECHNICAL
Technology information
With over 10,000 material formulations, we provide products tailored to meet specific purposes.
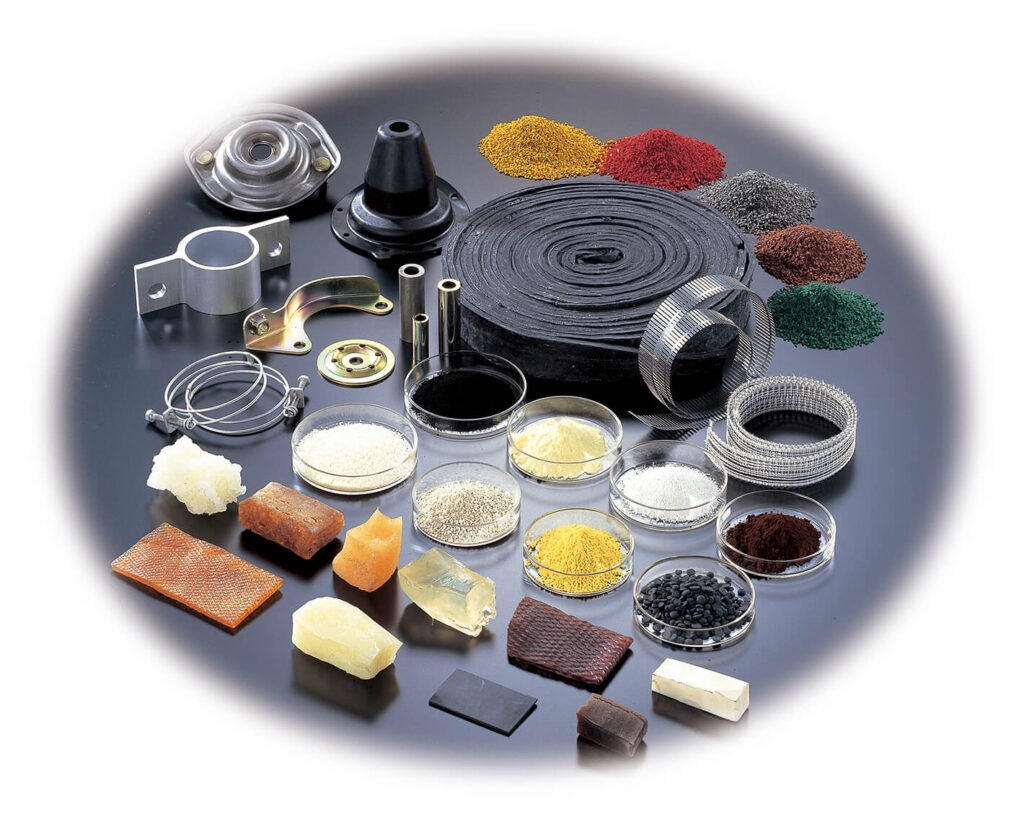
As a company specializing in the manufacturing of rubber and resin products for automobiles, we have grown alongside the development of the global automotive industry.
Examples
Body seal products
High-performance inside seal
A high-performance inner weather strip that is lightweight and highly resistant to wiping off glass fog using materials developed using resin foaming technology and water-absorbing fabric.
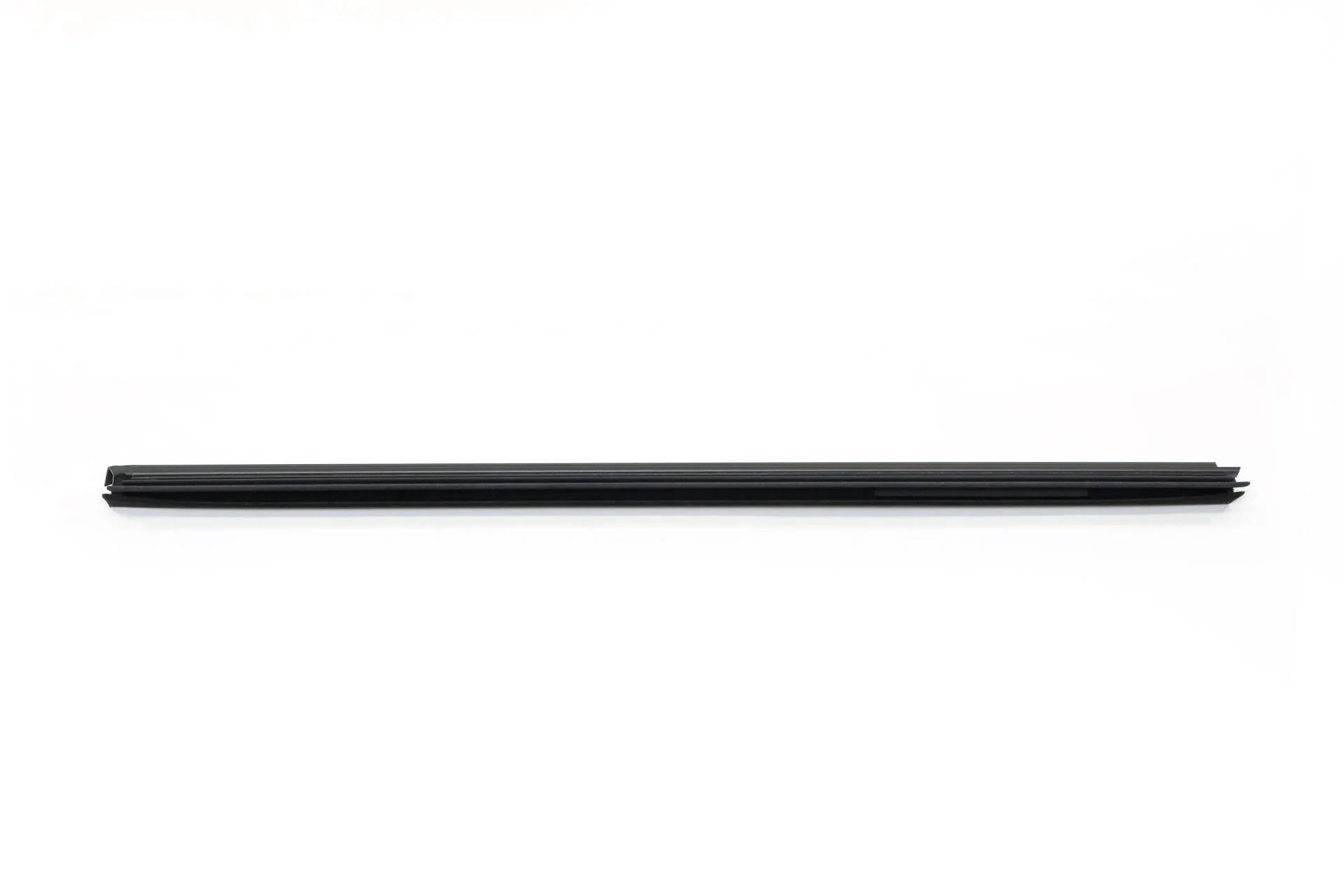
Stable foaming technology using thermally expandable capsules
Achieved weight reduction of resin core material by 30% (compared to conventional model)
・Improved sagging resistance by 11% Glass seal lip material and water-absorbing fabric make it easier to wipe away glass fog.
* Our experiment shows that the amount of water droplets left behind when raising and lowering the glass has been reduced by 50% compared to conventional methods.
High performance glass run
Glass run with improved noise resistance and glass flapping resistance that reduces deterioration over time.
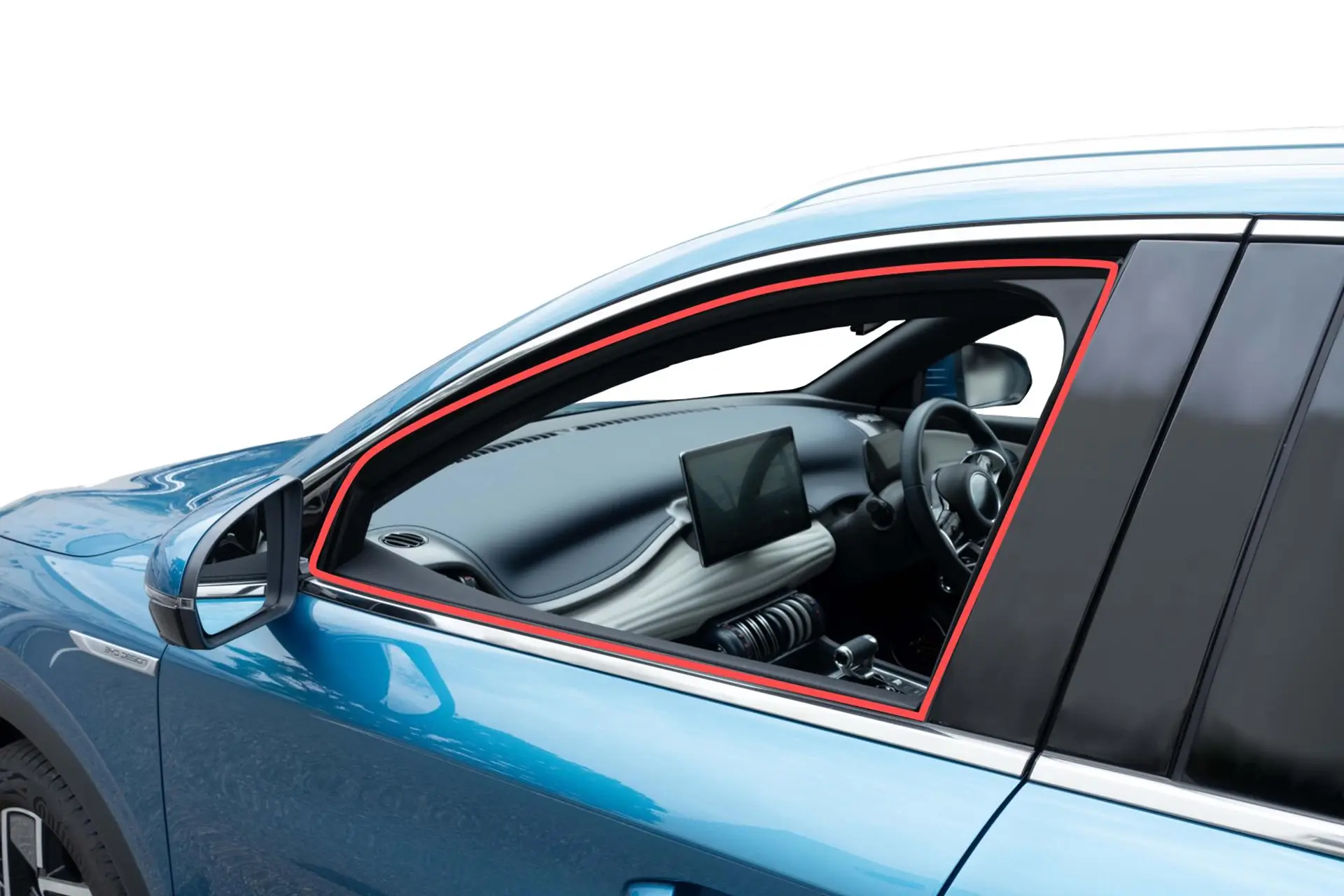
Achieving high performance with three new technologies (shape design, lip material, and high-performance sliding material)
・Anti-sagging performance improved by approximately 40% compared to conventional products, top class among TPV glass runs.
・Glass sliding resistance after durability test, an indicator of noise performance, has been improved by 30% (compared to our company’s comparison).
High-performance partition
Partition W/S that achieves a high level of improved vehicle assembly, scratch resistance, and weight reduction.
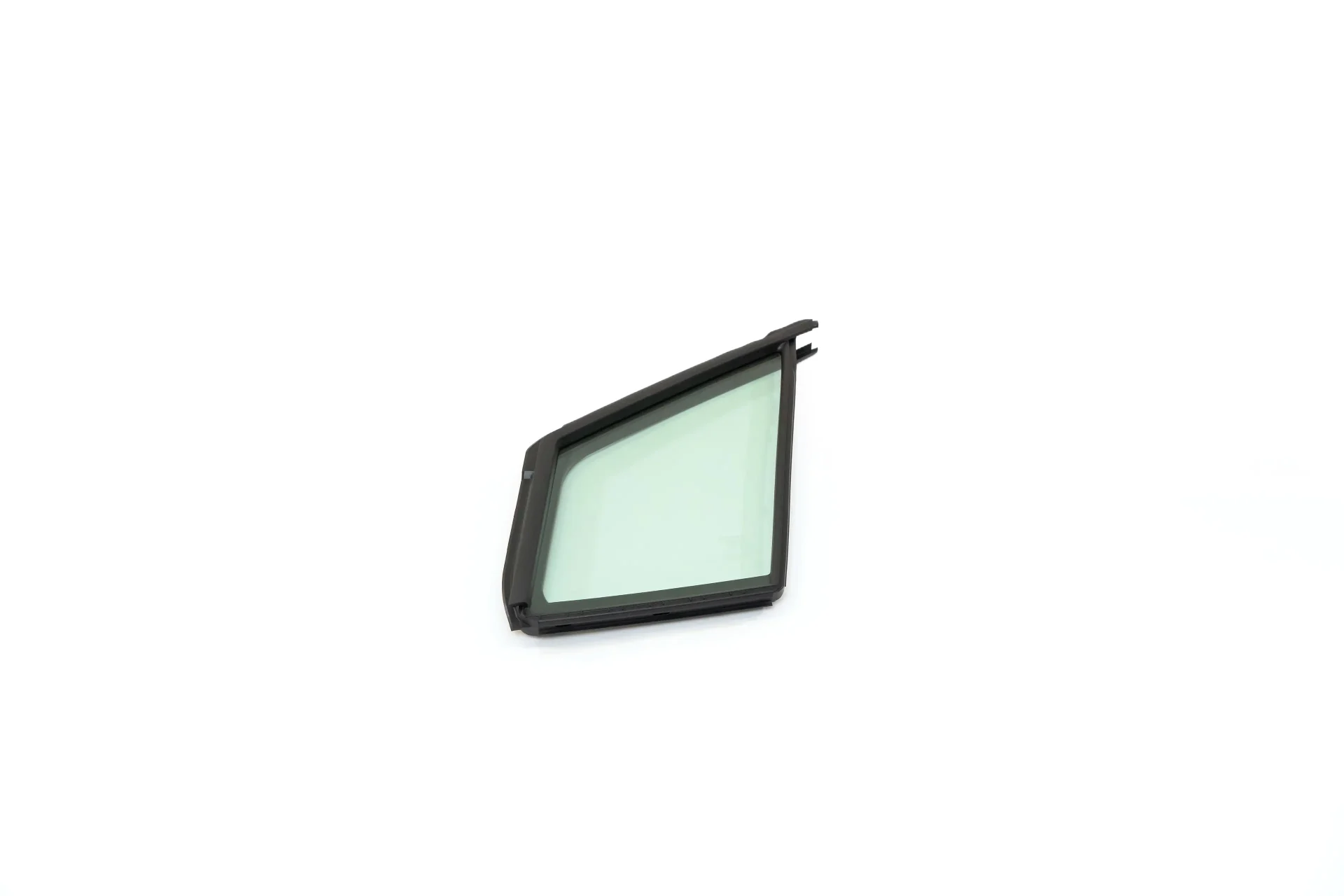
Developing new materials using special fillers and material compound technology (patented technology)
・Improves workability by reducing vehicle assembly force and improves adhesion with panels and surrounding parts. Low friction + lightweight, assembly force reduced by 40% (compared to our company).
・Due to the effect of special filler, it has better scratch resistance than PVC material. Prevents scratches during assembly work and ensures high quality design when using parts.
* PVC = vinyl chloride material, generally has excellent scratch resistance
TPV sponge sub seal
High appearance and high durability TPV sponge as an alternative to vulcanized rubber sponge.
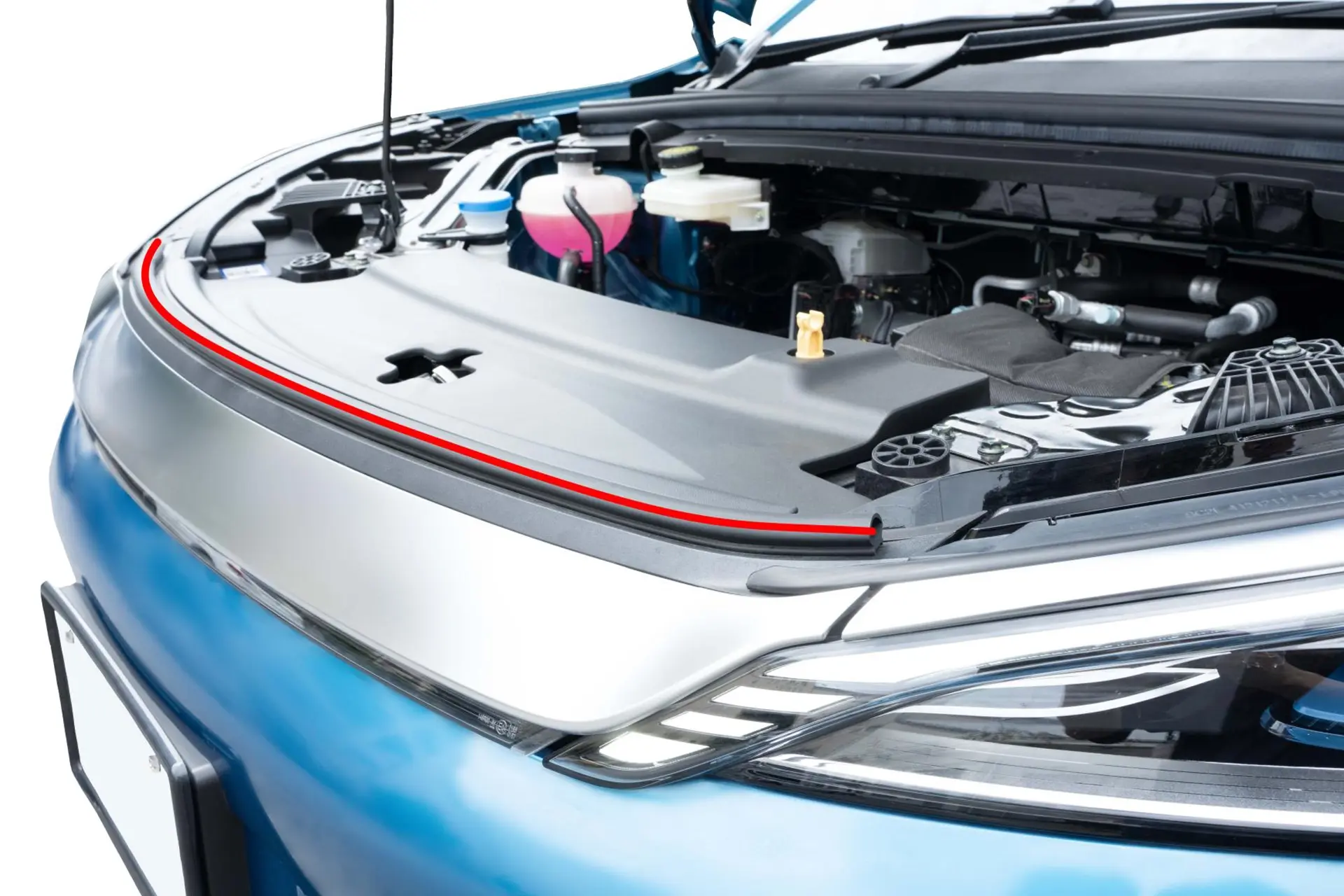
Achieved by foaming low-hardness materials using TPV foaming technology and using materials with good appearance and multilayer extrusion technology
・Recyclable TPV and energy reduction during parts production (-60% compared to our company), reducing environmental impact.
・Achieved prevention of release sound and high design (prevention of whitening) to improve defects in rubber sponge material.
Anti-vibration products
High heat resistant BUSH
BUSH using anti-vibration material with significantly improved heat resistance.
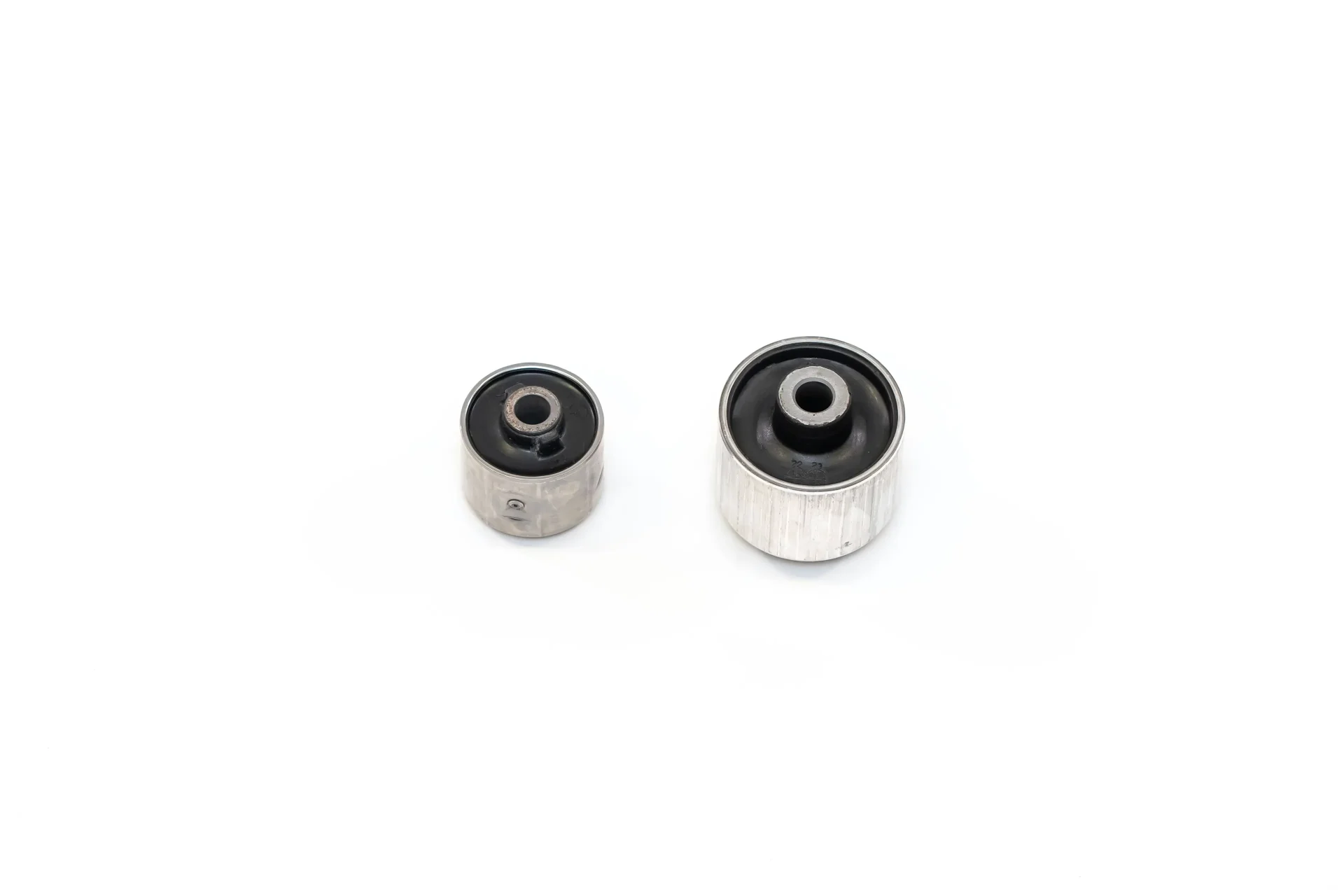
Through rubber material compounding technology and product design technology, we have achieved approximately three times the heat resistance compared to conventional materials (compared to our company).
・BUSH has anti-vibration characteristics that do not change over a long period of time, achieving performance that does not change the riding comfort over time.
Made of high heat resistant EPDM EXH/MTG
General-purpose rubber: EXH MTG, which is made of EPDM and is extremely heat resistant.
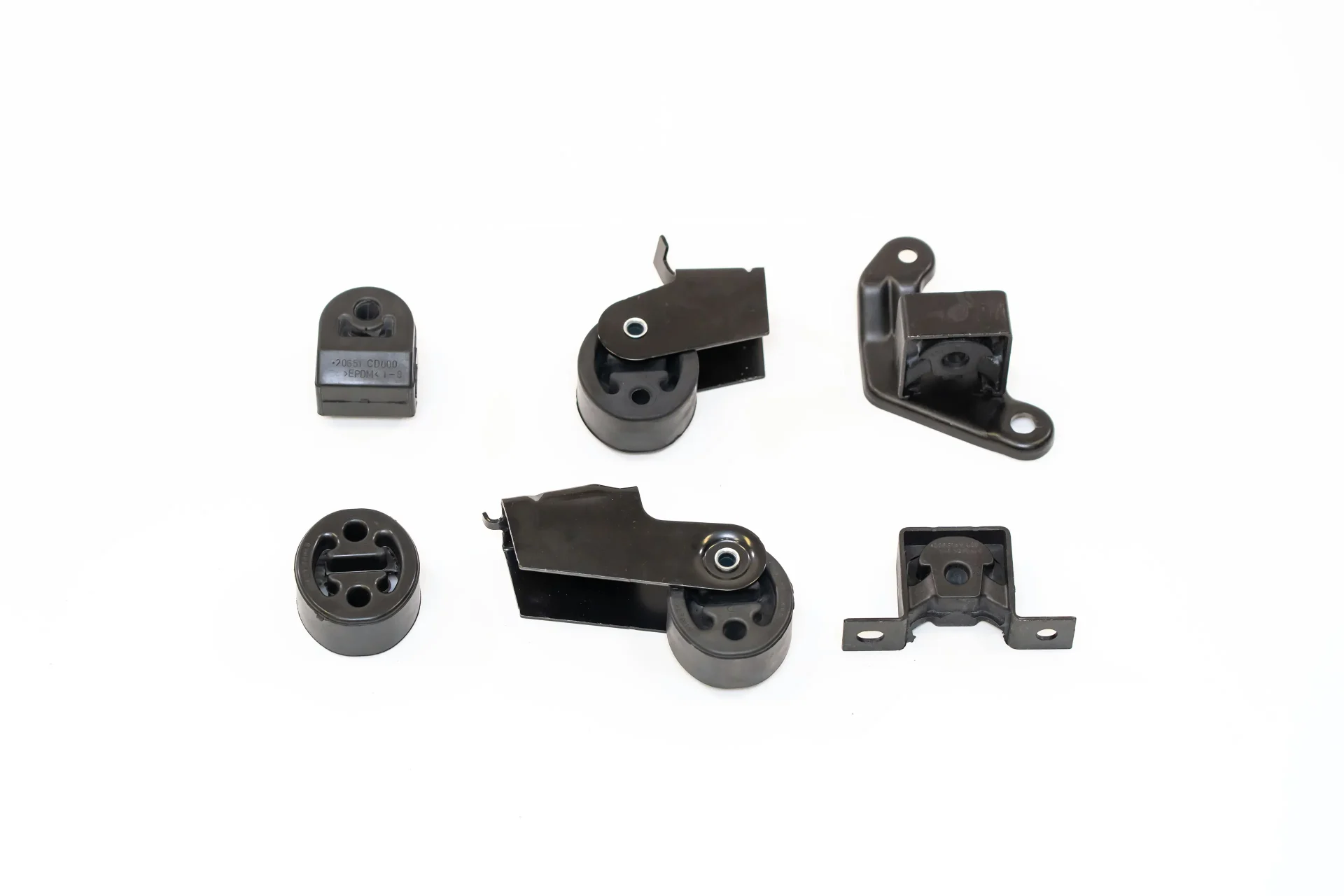
Achieved through the synergy of applying heat-resistant material technology for brake cups and design and manufacturing technology for vibration-proof parts.
・A general-purpose rubber that can withstand extremely high temperatures of 150°C or higher, which were traditionally the domain of special rubbers: By designing with EPDM, it offers higher anti-vibration properties and cost competitiveness than special rubbers.
Hose products
High electrical resistance water hose
Increasing needs for BEV/HEV cooling hoses: Hose compatible with high electrical resistance specifications.
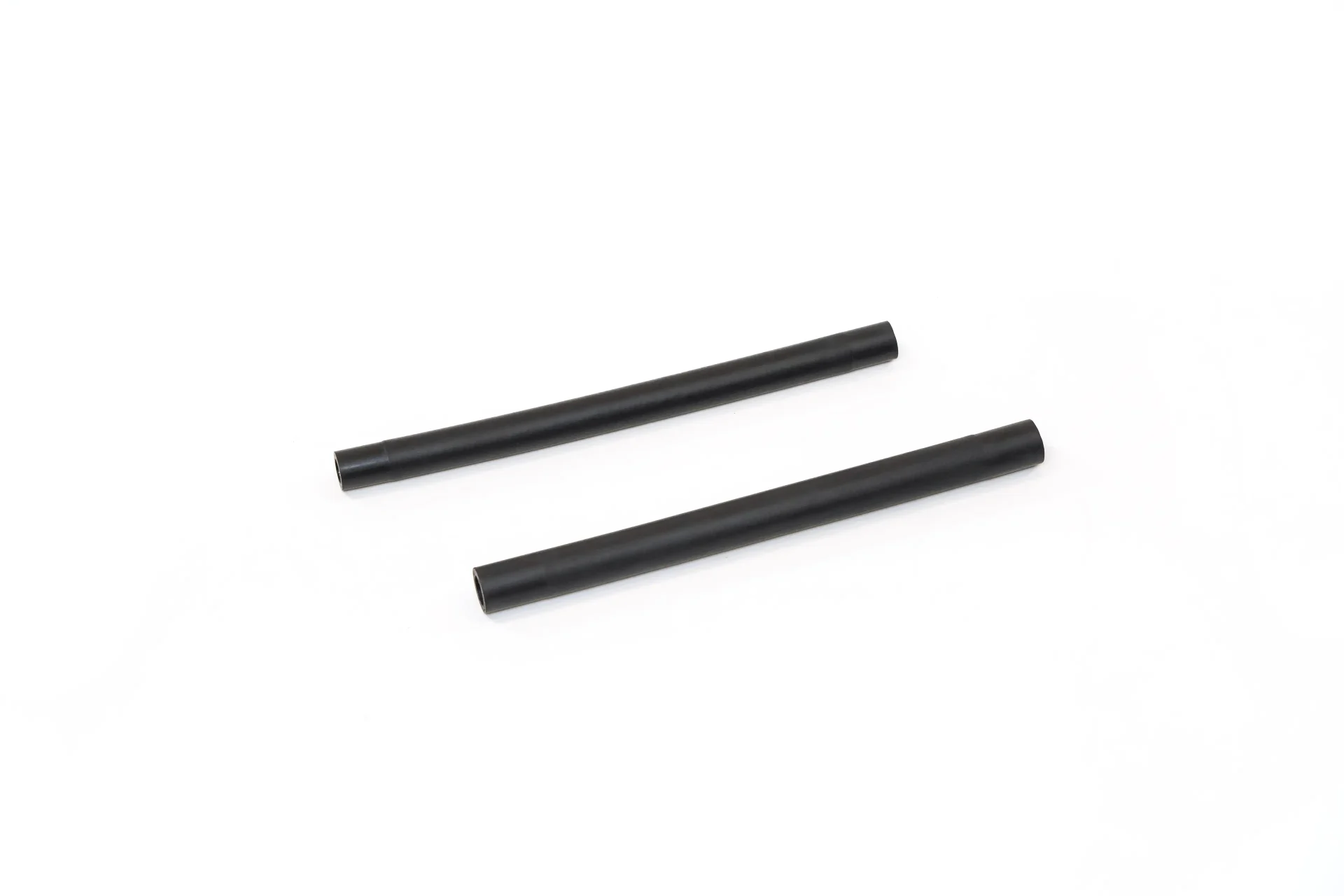
Realizing a water-based hose with high electrical resistance using rubber material compounding technology and hose manufacturing technology (patented technology)
・Provides highly functional hoses with improved corrosion resistance and lighter weight (compared to conventional models: no increase in mass) due to high electrical resistance.
Super heat resistant water hose
General-purpose rubber: Cooling hose made of EPDM that can withstand temperatures of 150°C or higher.

By optimizing the rubber material compounding technology and reinforcing threads, we have achieved a super heat-resistant cooling hose (2.5 times higher than our company’s)
・A lineup of general-purpose cooling hoses ranging from 100℃ to super heat-resistant specifications of 150℃ and above to meet the various needs of our customers.
Ultra pressure resistant water hose
Cooling piping rubber hose that meets the required specifications for high pressure resistance .(fastening seal performance)
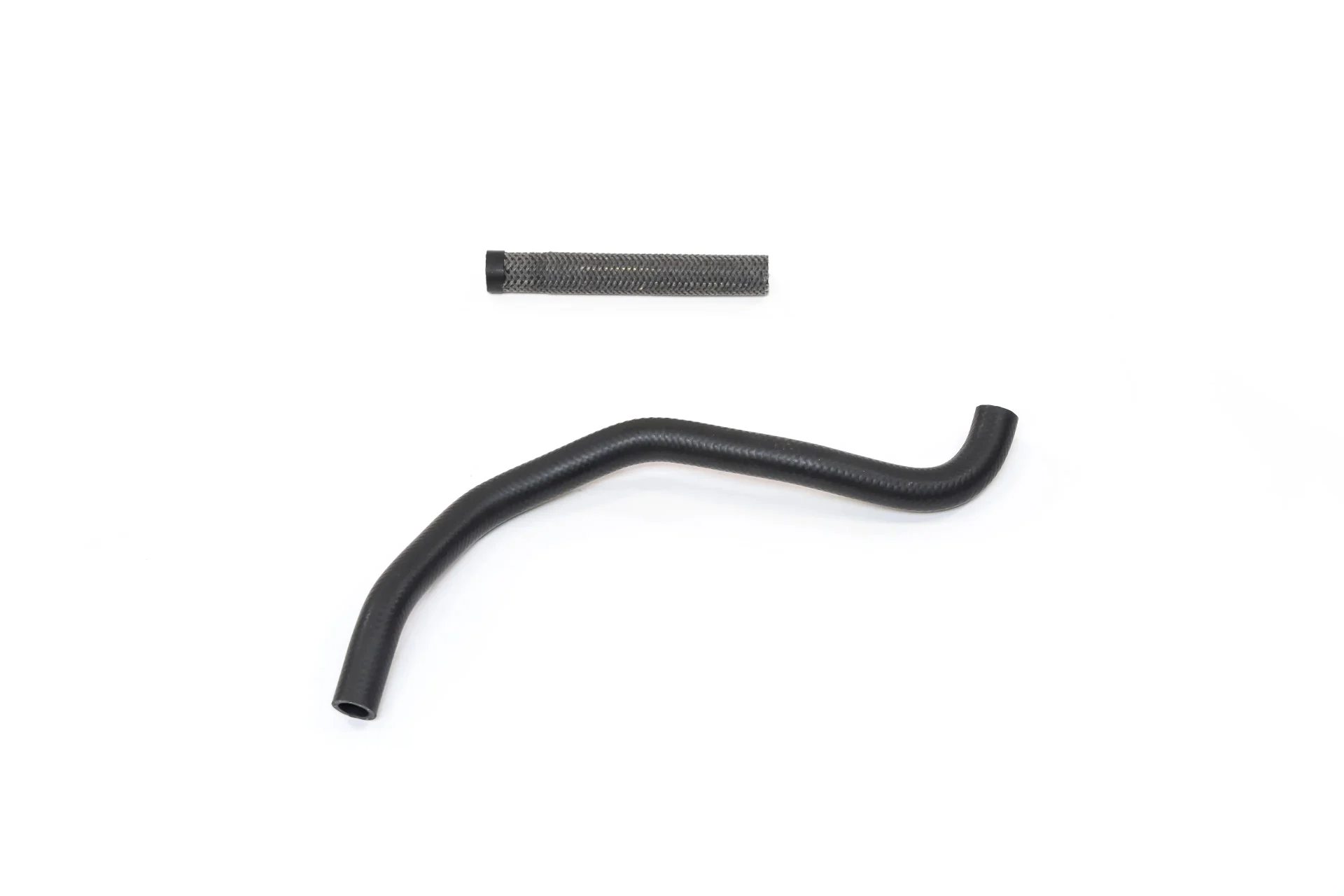
A pressure-resistant hose is realized by optimizing the type of reinforcing yarn and the weave angle, and combining materials that achieve pressure-resistant performance.
・For cooling system piping hoses, the pressure resistance is approximately twice as high as that of conventional products, without compromising the insertion process using optimized reinforcing threads.
Brake products
High performance master cylinder cup
Master cylinder cup with high durability, low temperature resistance, and low sliding performance.
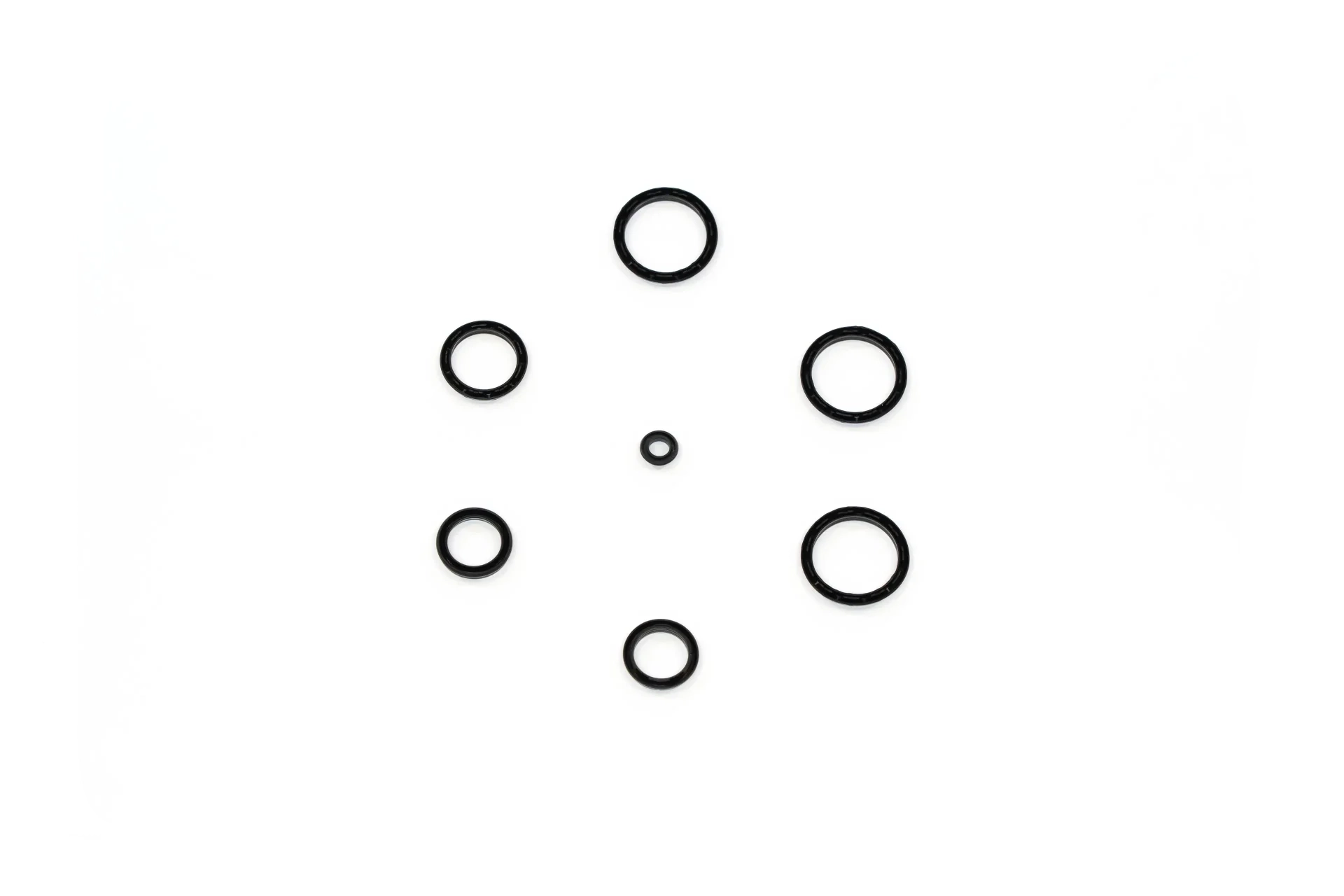
Achieved through fine mixing adjustments, special low-sliding material combinations, and thorough manufacturing condition settings.
・Durability has been improved by approximately 20% due to improved rigidity using the developed material. Can withstand high liquid pressure. In addition, the low sliding property, which is the opposite of rigidity, has been improved by 15%, contributing to improved brake feeling (compared to our company).
Technical ability
About our technology and quality
We are proceeding with the development of 3R* technology.
Our company is actively working on environmental issues by utilizing Kinugawa’s unique technology.
We utilize superior technology in a wide variety of ways, including reducing weight through resin and improving recycling rates. Please see below for environmental information.
*3R: A general term for the three Rs: reuse, reduce, and recycle.
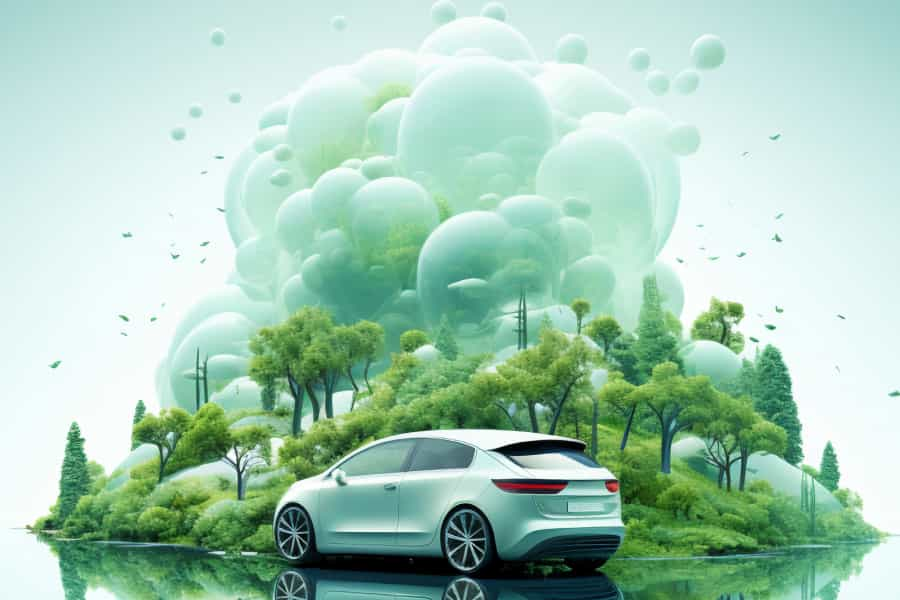
We respond to the various requests of our customers using industry-leading structural analysis technology.
The company has cutting-edge structural analysis technology and can respond to development periods and costs that meet the various needs of our customers.
Among these, we have a wide range of products, including our seal design technology that perfectly matches the complex panel structure of vehicle bodies and our structural analysis technology that guarantees durability and longevity.
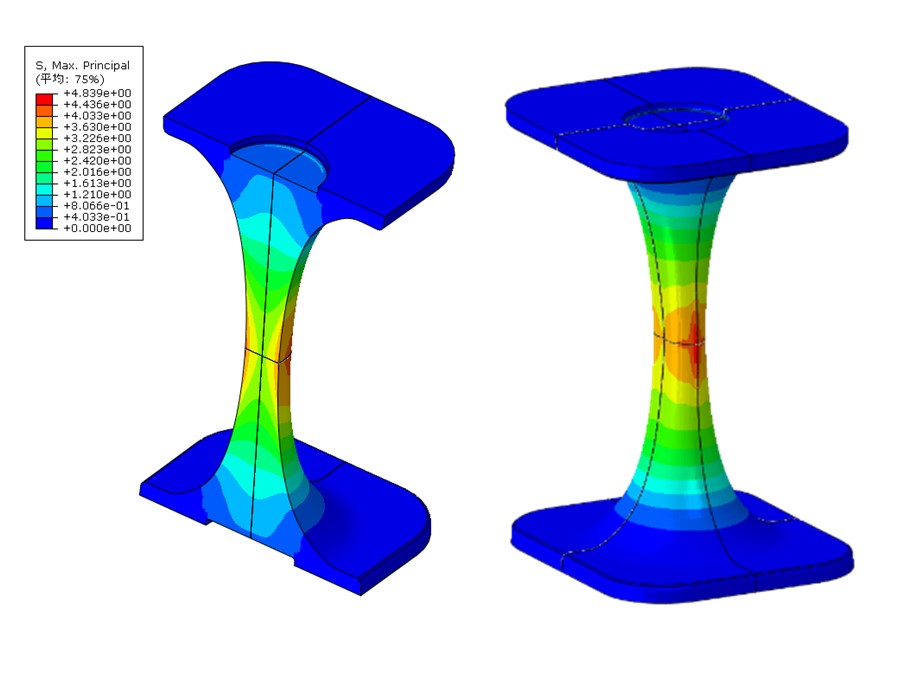
With our unique production technology, we are able to achieve high quality and low cost even for complex shapes.
Our company has reliable quality control that allows us to produce more than 100 million brake cups per year, as well as highly efficient, low-cost production technology using an unmanned (fully automated) integrated line.
In addition, we have built a global production system centered on Asia (China, Thailand) and North America, and are able to provide products of the same high quality at all production sites.
Flexible production system that can flexibly respond to changes in volume
Grass run, one person food stall production line
Highly efficient, low-cost production technology using an unmanned (fully automated) integrated line
Bush manufacturing, new cell line
Precision processing technology and quality assurance system unique to a factory designated for important safety parts
Brake cup injection molding automatic integrated line
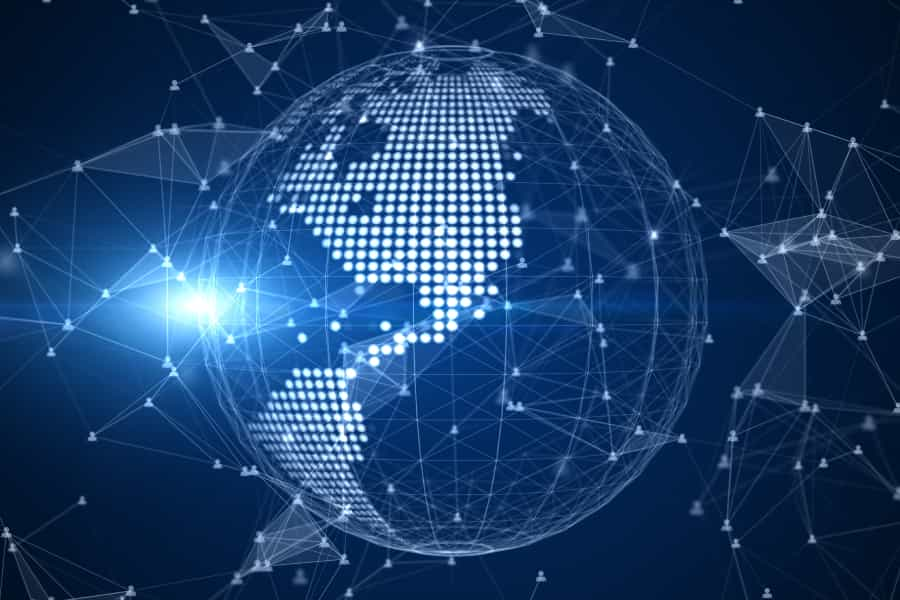